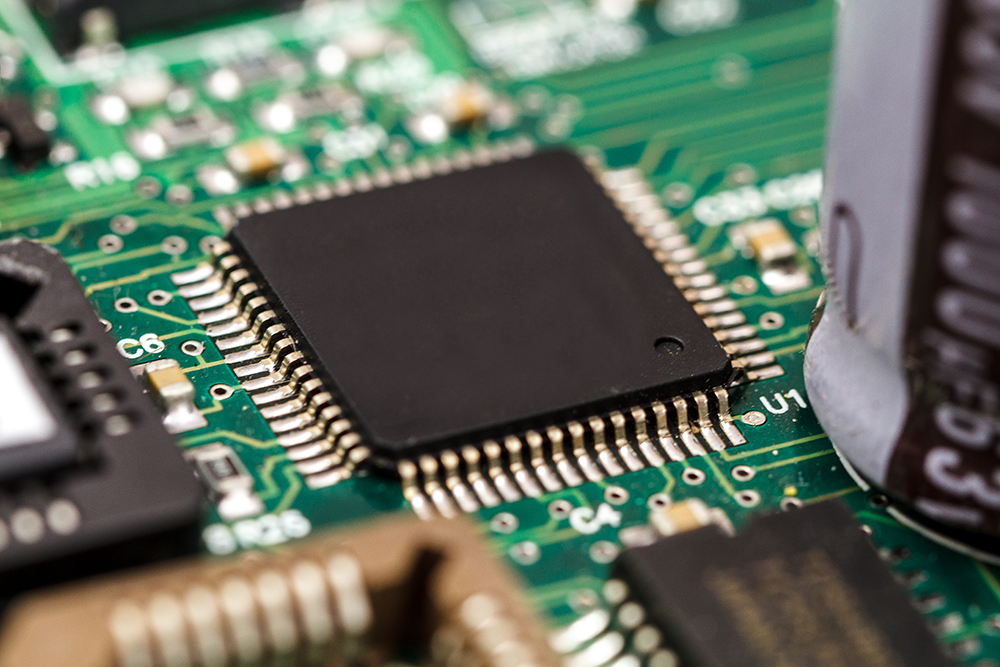
The supply chain is just like any other chain – each link needs to work well in order to ensure its overall strength. That’s why when demand for component production began vastly outstripping supply, and shipping times started rising (and rising), the whole globe felt the repercussions.
For many years, plenty of manufacturers have adopted a ‘just in time’ approach – first popularised over in Japan and then integrated into the Western business world many decades ago. When it works, it’s a great way to minimise the space a manufacturer needs, by only ordering components when required, and streamlining their processes to ensure the finished product goes out of the door as swiftly as possible.
The problem comes when there are unforeseen circumstances which come into play, and delay (or even completely stop) those components being delivered to the manufacturer in the timely manner needed to keep the system flowing.
And when there’s not just one problem, but multiple, happening all at once across the globe? It has the potential to become a crisis – unless ITS businesses respond quickly and retain as much control as they can over the situation.
The background
While we’re all acutely aware of the impact of the pandemic, it would be remiss not to explore the reasons behind the supply chain problems we’re experiencing without mentioning coronavirus and its associated lockdowns and restrictions, which have caused havoc to component producers everywhere.
The workforce in Taiwan, Malaysia, China and other Asian countries which supply the majority of integrated circuits (ICs) and other important components has been affected on and off for two years – at some points, resulting in a 50% throughput in lots of factories compared to pre-Covid levels.
Another factor has been the leap in demand for these sorts of components, caused by a continued increase in the consumer electrical device market and the rise of the electric car (6.4 million were sold worldwide in 2021 alone, even with the pandemic and the problems with IC production).
The developing situation in Ukraine may also have an impact on sectors including ITS, given the country manufactures a huge proportion of the world’s neon (used in semi-conductors) while Russia is responsible for the production of a third of the world’s palladium (used in sensors and memory products).
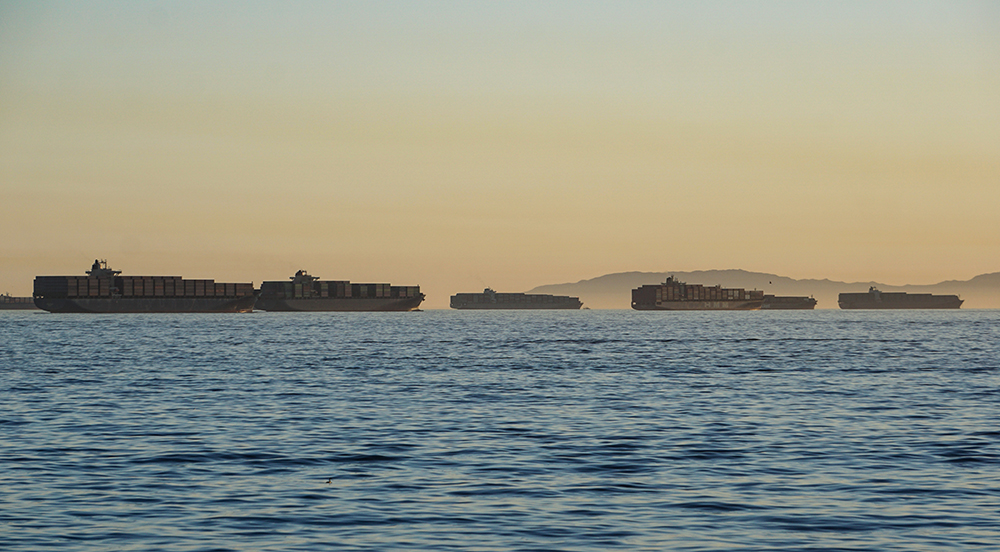
We’ve also seen energy prices soar. Taking China as an example, the government there issued restrictions limiting the amount of electricity which could be produced using coal, at the same time as importing coal became much more costly. Instead of passing on these price increases to their customers, the Chinese electricity companies took the view it would be better to ration not only domestic users, but industrial customers too.
The resulting scenes have been reported by news outlets everywhere: irate factory bosses claiming they’d only been given a few hours’ notice that they were unable to open up the next day; employees sat on pavements waiting to be told their workplace was reopening; and factories in two-thirds of China shutting their doors for hours or even days at a time.
Manufacturers such as Texas Instruments are already planning new fabrication plants in the US (known as fabs) in order to increase the number of components they can produce.
While this may solve the supply/demand problem once the fabs are up and running - there’s also been a real problem with the next link in the supply chain: shipping.
At AGD, we’ve seen some order lead times shoot up from eight weeks to more than a year – representing a 600%+ increase. And we’re not alone: the pandemic has pushed up shipping times on almost all routes, and extreme weather has also played its part in contributing to the problems.
Experts have calculated more than three-quarters of ports in the world have increased turnaround times, and the boss of a leading global shipping group described it as ‘one gigantic bottleneck’ – not a hopeful description for those ITS firms relying on components being delivered to them.
And it’s not even simply a case of getting past the hurdles of having products arrive in the UK; our British ports have stacks of containers waiting to be transported to their end destination. That’s down to the shortage of around 100,000 lorry drivers as a result of Brexit.
The outlook
Given we’re now two years into a pandemic that was expected to cause restrictions for a few weeks, it would be foolish to pretend we can predict the exact date problems may end. But what’s clear is that there is no easy fix.
Re-establishing the sort of throughput that allows component makers to keep up with the current demand, and scale up as that demand continues to rise – that takes time.
Restrictions across the globe are slowly being relaxed but, once again, it will take time to establish the sort of ‘new normal’ we’ve all been talking about since mid-2020.
And the scores of ships waiting to dock and stacks of containers waiting for a lorry to pick up their contents – those queues will have to be gradually reduced until there’s no longer a bottleneck.
The response
In the short term, adjusting lead times and liaising even more closely with customers to keep them updated on lead times was the only way ITS companies could really respond to the issues which the world was beginning to face.
But once it became apparent that the situation wouldn’t resolve itself in a hurry, the focus became mitigating against the huge waiting times between ordering components and receiving them – because a year’s wait is simply not a viable way to continue doing business.
We made the decision to double our investment in stock reserves, and begin looking much further ahead – typically between 18 and 24 months – when placing orders for silicon, printed circuit boards and other components for our products.
It’s a difficult balancing act, because nobody wants to be left with components outnumbering their product orders. But having components on hand that can be used to manufacture a product with no waiting around for weeks, months or even a year – that puts an element of control back in the hands of the ITS company, rather than relying on production lines halfway around the world, or complex and backed-up shipping systems.
There’s also a lot to be said for increasing conversations with customers around what their plans are going forward. While highways authorities and other transport bodies are unlikely to be able and willing to commit to specific orders that far in advance, they will have plans for upcoming projects which, when shared, make it much easier to make educated calculations about how much stock you’re likely to need. This approach also gets ITS manufacturers and their customers into a habit of having much earlier and more in-depth conversations around future plans and projects.
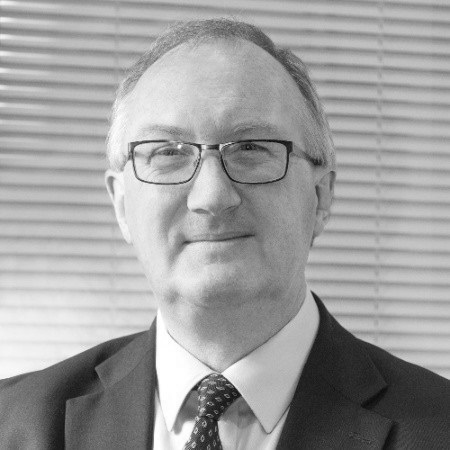
Many of the causes of the current supply chain woes are completely out of the hands of the ITS sector, and we’re looking at a slow recovery – but mitigating against the worst of the problems with a mind-set shift from ‘just in time’ to ‘well in advance’ is, I believe, the best way that we can take back some control. Planning in advance and holding larger stock reserves isn’t just the answer to 2022’s problems - moving forward it’d be a great way to retain a better handle on lead times, project planning and stock control.
Just like we’re hoping to leave Covid, lockdowns and port queues behind, let’s leave ‘just in time’ behind, too.
About the Author:
Ian Hind is commercial director of AGD Systems, which manufactures ITS products including pedestrian and vehicle detection and monitoring radars .