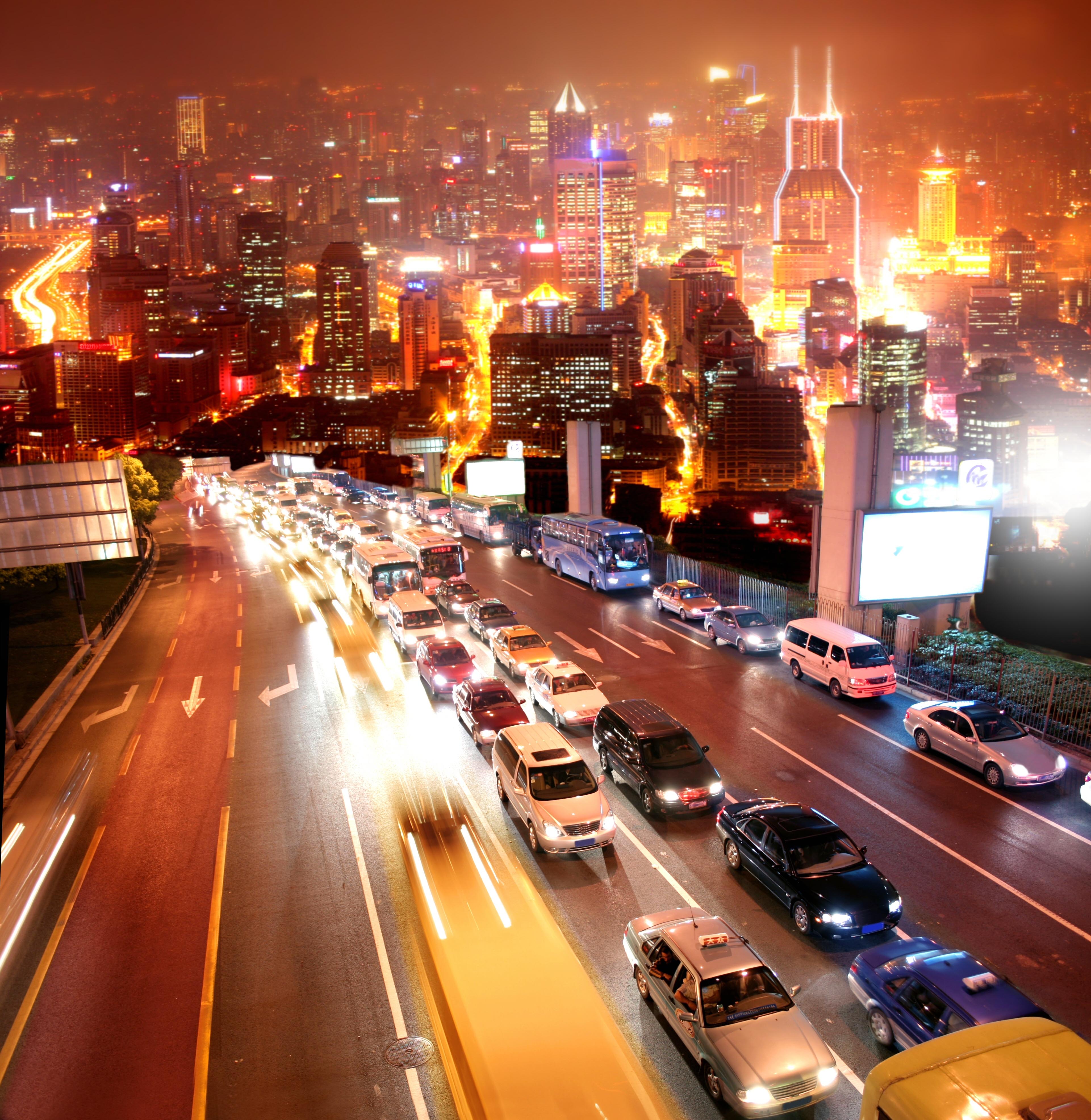
The adaptation of machine vision to transport applications continues apace.
That the machine vision industry is taking traffic installations seriously is evident by the amount of hardware and software products tailor-made for ITS applications that are now available on the market. A good example comes from US-based
Beyond the standard traffic management and incident detection, the horizon to horizon view gives users additional data collection capabilities as it tracks objects through the intersection and the system reports in which direction vehicles and cyclist head. The company’s vision processing algorithm automatically counts vehicles and measures intersection performance 24/7. According to the company, such long-term counts provide a more accurate understanding of the intersection and how it is affected by seasonal variation, weather and other factors that will not be apparent in the traditional 24-48 hour studies.
Another example is the
The standard 6mm lens provides a 55° horizontal field of view, while fitting the 3.6mm version widens this to 87°.
Another US company,
Video content for typical red light violation detection systems is transmitted from the intersection to a centralised facility for time-consuming manual review by operators to distinguish violators from the innocent.
Eutecus used a Camera Link version of
In this application, the camera provides the primary video analytics source, monitoring both the traffic light and the traffic itself.
Andrew Herson, senior manager at Eutecus says: “The Genie camera essentially ‘maps’ distinct images of the traffic light as well as images of the vehicle in relation to the intersection stop line. This scene analysis is combined with data from radar, and a second, low-resolution video camera provides documentation that can be used for verification in the event a driver disputes a ticket.”
According to Euctecus, the system only sends pictures to the operator if the images of the traffic light and vehicle/stop line don’t align as they should - thereby indicating a violation. The operator then confirms the violation and generates a ticket without the need for a lengthy or exhaustive video review.
It says the automated nature of the solution eliminates the potential for human error and increases overall system reliability, and adds that it can capture and process multiple simultaneous events, such as two cars running a red light at the same time.
Streamlined solutions
As the system’s ‘intelligence’ is embedded with the camera, the entire solution can be installed above ground which Herson says provides municipalities with a streamlined and far less costly solution than traditional traffic monitoring applications. Beyond red light violation, the system is said to be suitable for applications including toll enforcement, speeding detection, wrong-way driver detection, stopped-vehicle detection and as a traffic light sensor.
Geoff Collings, Vysionic’s sales and marketing director said: “Using the machine vision to detect the flashing red light on the signs makes our system non-invasive, so we do not have to break into the railway’s safety critical signalling system.”
Beyond capturing offences, the radar part of the system can gather blind data including counting vehicles, cyclists and pedestrians and classifying vehicle type into car, van and truck.
Data transmission
While machine vision helps reduce the amount of data being transferred over the network, the ever-growing number of installations means capacity limitation remains a concern.However, the latest CoaXPress standard for HD-SDI, USB, GigE or Camera Link, defines a high-speed interface between a camera and a processing device, such as a frame grabber, and offers better performance than traditional analogue.
In its simplest form, a single coaxial cable is sufficient to transmit data at up to 625 megabytes per second, to simultaneously transmit control data and triggers, and to provide at least 13W of power to the camera. Where even higher data transmission rates are required, four parallel cables can be used to provide rates of up to 2,500 megabytes per second.
According to Jean-Bernard De Bal, vice president of business development at image acquisition and software supplier
Signal latency is another critical consideration for vehicle tracking and highway control applications and here again the CoaXPress standard can be useful as it allows the transfer of uncompressed video so zero latency is possible. High frequency real-time triggering and exposure time adjustment can also be accommodated.
CoaXPress connections can be made using the same heavy-duty coaxial cables used for analogue and HD-SDI cameras allowing analogue cameras to be replaced with high resolution digital units using the same cable network, making upgrades cheaper and easier. And as the thick copper cable inside coaxial cables is protected from electromagnetic interferences by a Faraday cage, they perform in the harshest environments and are able to withstand shocks and vibrations.
The CoaXPress standard also allows higher cable lengths compared to standards such as Camera Link or USB and lengths of greater than 100m may be achieved at half speed and greater than 40m at full speed.
While the latest software, cameras and networking may better suit traffic applications, the basis of everything remains the image sensor. Earlier in the year the machine vision sector was set unsettled by
While many favour CCDs for noise-free and geometrically accurate image of moving vehicles needed by the ANPR algorithms, according to sensor manufacturer
Another reality of traffic application is the need to perform tasks during daylight, low sun, darkness and in extreme climatic conditions. Beyond reliable ANPR, the authorities also demands colour information and sometimes recognisable images of the driver and for those reasons many manufacturers including e2v offer both colour and monochrome versions of their sensors – the latter with infrared wavelength capabilities.
Although over recent years CMOS sensors have been taking an increasing share of the traffic camera market, Sony’s plans to cease CCD sensor production (others may follow) may cause concern in some authorities. The advice from
Imaging Development Systems (
The number and duration of the integration periods can be set by hardware or software and according to the company the resulting blurred image can be reconstructed to allow detail such as number plate information to be obtained. In addition, image processing can be used to calculate the speed of the object and whether it speeds up or slows down by taking into account the number and length of the integration periods and the distance covered across the sensor.