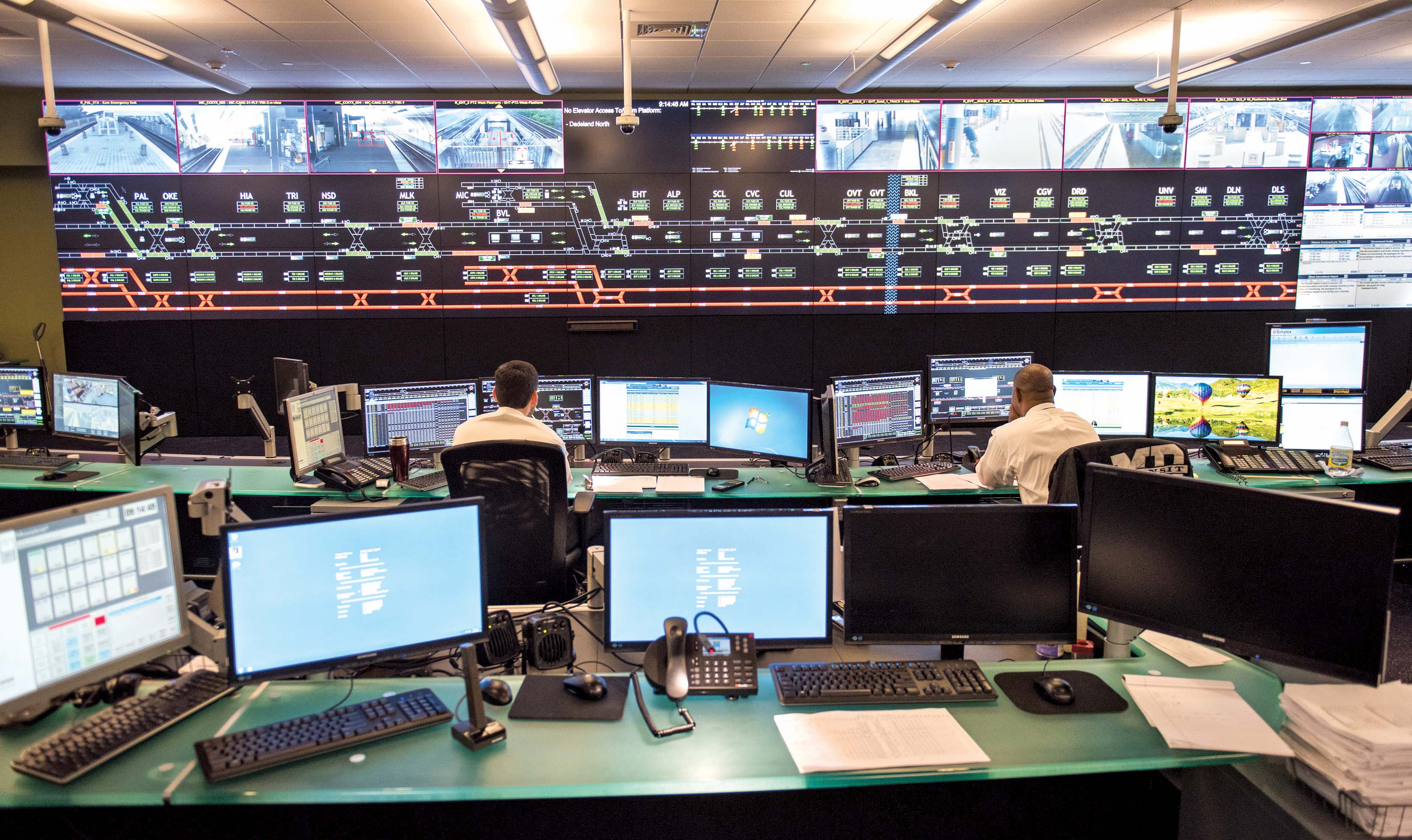
Jason Gomez and Daniel Mondesir describe how passenger disruption was minimised during a major upgrading of the control room of Miami-Dade’s Metrorail.
In 1984 when the Miami-Dade Department of Transportation and Public Works’ (DTPW) Metrorail system was launched in southern Florida, trains ran 18km along a single line and stopped at 10 stations. Today, the DTPW Metrorail is a 40km-long dual track, elevated transit system with 136 rail cars and 23 stations – including services to Miami International Airport, one of the largest international hubs in the US.
There has been a surge in new developments built near the Metrorail over the last few years and ridership has increasing almost five-fold since the line’s inception.
This increase has pushed the limits of the now-ageing infrastructure and none more so than the Metrorail control system. The inflexible design of the old control system restricted DTPW’s ability to upgrade or add new Metrorail stations; any upgrades had to be awkwardly tacked on to the existing control consoles which created a very disjointed system architecture. The control system was also becoming difficult to maintain due to its reliance on obsolete parts, and an additional repair contract was needed to just keep things running reliably.
Clearly Miami was in need of a more modern control system using the latest technologies in workstations, computer servers, Ethernet and fibre networks, phone systems, video displays, control software and other systems.
Following a tender process DTPW selected and worked with B&C Transit to create a custom control system for the Metrorail. The result is a forward-looking solution that streamlines day-to-day operations, improves reliability and supports future expansion.
With the new control system the rail traffic controllers, managers and maintenance personnel can communicate important information to passengers on the trains and platforms as well as view and control all rail operations from any workstation on the network.
Service continuity
Central to the upgrade was the construction of a modern control room. Being the primary contractor, B&C oversaw the design and construction of the new control facility which now occupies the floor space of the original control room plus an adjacent office.
As the Metrorail system is a vital transit route for passengers in and around the Miami area, the system needed to be upgraded without any service interruptions and this was achieved by phasing in all new construction, testing and commissioning.
Initially a new control room was built in the unoccupied office space adjacent to the existing control centre with sound and dust barriers erected to safeguard the operations and minimise interference with the control room’s ongoing work. This new facility includes a large-scale video wall with 36 new 55inch (1.4m) monitors in a 3x12 configuration to provide controllers and managers a concise overview of the state of the entire system, including train control, traction power, streamed high-resolution images for monitoring and general station summary information. A section of the video wall is dedicated to increased security capabilities with recorded image playback, camera control, alarm monitoring and live viewing.
Once the new control centre was constructed, new consoles and computer hardware were installed in the area and connected to a new Ethernet network that was installed to provide communications from the control centre to the stations, in parallel to the old network. DTPW then ran the Metrorail in dual-operations mode with all indications and controls displayed by both the new and legacy systems to ensure full duplication and compatibility. By running both systems at the same time, the new control system could be tested and verified during the day or night without affecting passenger service — redundancy was maintained during peak hours and any disruptive tests were performed during off-peak hours. B&C performed local testing of each individual subsystem, followed by an integrated test in which all subsystems were tested as a complete functioning system. Finally, the new control system was used to continuously control the Metrorail for an extensive demonstration period of 1,200 hours.
After all safety certification requirements were met, operation of the Metrorail was fully transferred to the new control system and the legacy control system was removed. B&C then constructed non-critical facilities in the original floor space, including a viewing gallery, offices and break rooms. The new control system was built and thoroughly tested without causing any service interruptions and has been running smoothly since completion in October 2015.
Non-proprietary
At the heart of the new control system is the fourth generation of B&C’s Nucleus control system software which offers major advances over its predecessor in terms of programming language, stability and resilience. Based on fifteen years of transit-specific software design, B&C customised its latest software to match DTPW’s needs and improve operational efficiency.
The Nucleus software unifies subsystems that typically have different interfaces into a single application — including train control, supervisory control and data acquisition (SCADA), traction power, scheduling, closed circuit TV, variable message signs, public address system, elevators and escalators. As such the system addresses virtually all the rail traffic controllers’ daily needs.
Point-and-click software allows the traffic controllers to drill down and view specific areas of the system, monitor alarms for all subsystems globally, track and route trains and communicate with trains, stations, and commuters throughout the station via voice and visual announcements in real-time using a single control console.
The new public address system delivers audio and visual communications to passengers on platforms and other station locations. Messages can be created in multiple languages with audio generated from workstation microphones, pre-recorded media files or using Nucleus’ ‘text-to-speech’ function. The messages can be created, edited, scheduled and played at select locations with assigned priority levels. The existing radio system still provides communication to the drivers and passengers inside the trains, as required.
Redundancy
As the Nucleus central control system is integrated with the Metrorail’s maintenance and operations control system, the maintenance yard can be monitored from the central control room and the mainline can be monitored from the yard. This enhances communication between the rail traffic controllers and yard control personnel, which both increases operational efficiency and ensures the accuracy of real-time train tracking as trains exit and enter the mainline. In case of an emergency this integration also allows controllers from either location to control the system.As implemented the control system has triple hardware redundancy. The central control facility houses the primary and backup computer servers and database. If the primary server loses communication or fails for any reason, the backup server will seamlessly take control of the updates to the database. An additional database and server is housed at the maintenance facility, along with dual 70inch (1.8m) overview monitors and a dual monitor workstation. So DTPW can easily operate and control its entire system from this alternate location, even if the central control centre is shut down.
B&C’s non-proprietary Nucleus software reduces the time and complexity involved in making a change to any program, which facilitates both maintenance and any future network expansion. Specialised infrastructure incorporates both hardware and software redundancy to ensure uptime for mission critical operations. The new control system also automatically notifies in real time engineering and maintenance personnel of any failure that can impact service, before the controllers sometimes notice the problem — a significant operational improvement to the 20 minutes or longer needed for the old control system.
By understanding specific DTPW’s requirements B&C was able to improve transit in Miami-Dade County by creating a larger, technologically advanced control centre capable of supporting current operations, as well as its plans for future expansions.
The next step in modernising DTPW’s Metrorail system is the replacement of all 136 Metrorail cars by 2019. The county is using its half-cent transit tax to update the old fleet that went into service in 1984. The new cars will feature many new amenities, including Wi-Fi, LED lighting and bike racks. Other upgrades include a new generation of station cameras that include sensors to detect anything on the track. So if there is any unauthorised object or person on the track, the system will automatically relay that information to the control centre.
- ABOUT THE AUTHORS: Jason Gomez is the vice president of engineering and Daniel Mondesir is a senior engineer at B&C Transit.